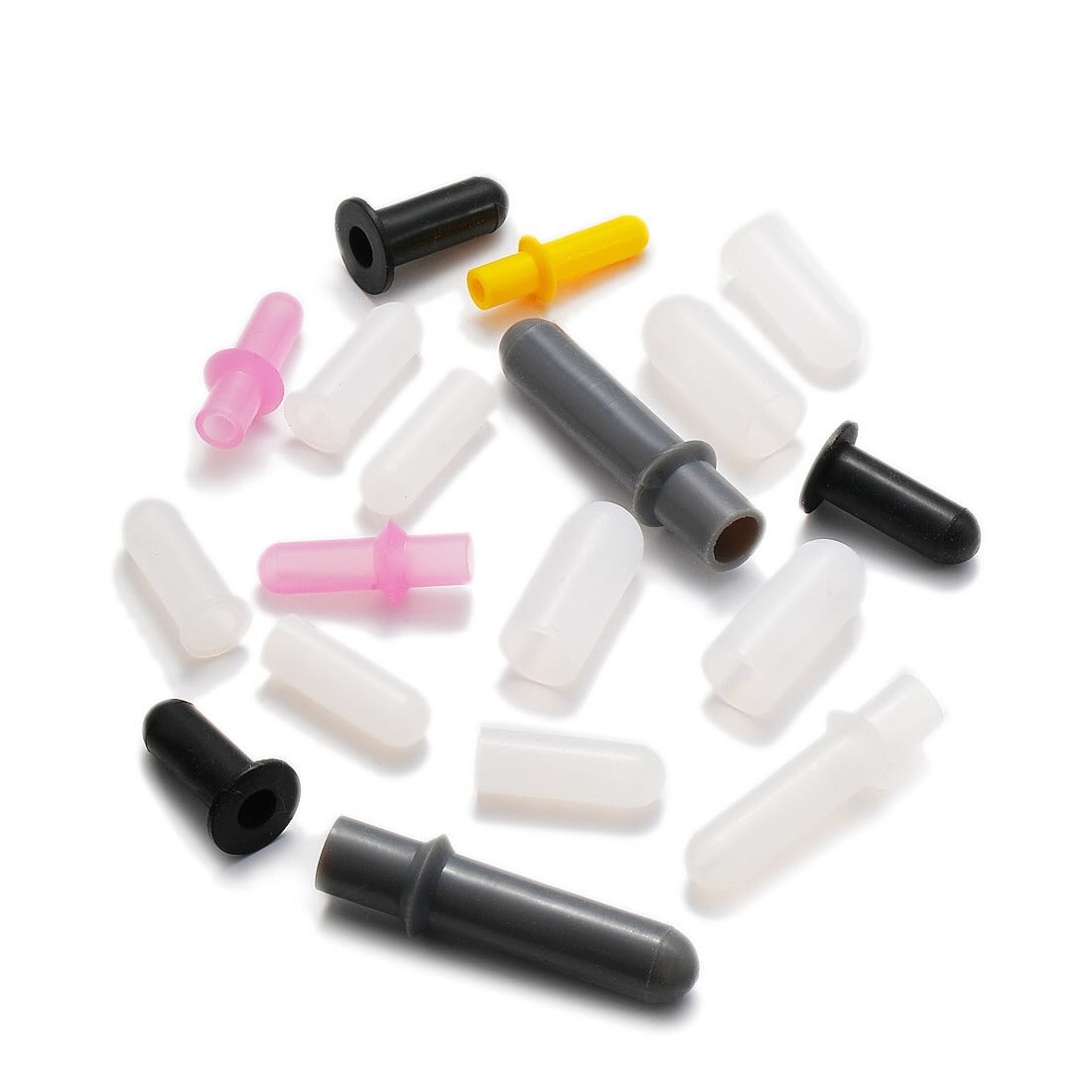
Guide to Silicone Plugs and Caps for Masking Applications
Share
Silicone plugs and caps are widely used in high-temperature masking applications for coating processes such as powder coating, e-coating, anodizing, and plating. These masking solutions are designed to protect specific areas from unwanted coatings while withstanding extreme temperatures and ensuring clean finishes.
This guide provides an overview of the various types of silicone plugs and caps, their specific designs, and their practical applications.
> Shop our portfolio of silicone masking solutions
Silicone Plugs: Types and Applications
1. Silicone Tapered Plugs

Design and Functionality
Silicone tapered plugs feature a conical shape, allowing them to fit a range of hole sizes while maintaining a tight seal. Their high-temperature silicone construction makes them reusable and resistant to extreme heat.
Typical Masking Situations
- Masking threaded and non-threaded blind holes in powder coating, e-coating, and anodizing
- Providing a secure fit to prevent leakage or seepage during plating
- Withstanding high-temperature curing processes without degradation
- Offering reusability for multiple coating cycles
> Masking Supply Tapered Plugs
2. Silicone Pull Plugs

Design and Functionality
Silicone pull plugs are designed for through-hole masking and feature an extended section for easy removal. They provide a leak-proof seal and are particularly effective in applications where both entry and exit points must be protected.
Typical Masking Situations
- Sealing through-holes in powder coating, e-coating, and plating applications
- Masking threaded holes on both ends to ensure no coating buildup
- Ensuring fast and easy removal after the coating process
- Withstanding high-temperature oven curing
3. Silicone Flangeless Plugs

Design and Functionality
Flangeless silicone plugs, also known as ribbed plugs, are designed with a textured exterior to enhance grip and prevent displacement during high-temperature masking processes. The absence of a flange ensures they do not interfere with surrounding surfaces, making them ideal for masking surfaces right up to the hole.
Typical Masking Situations
- Masking deep-threaded blind holes where a secure grip is required
- Preventing blowouts during high-heat curing in powder coating
- Providing a firm seal in automated finishing processes
- Withstanding chemical exposure in anodizing and plating
> Masking Supply Flangeless Plugs
4. Silicone Chamfer Pull Plugs
Design and Functionality
Chamfer pull plugs are specifically engineered to provide an effective seal over leading threads and chamfered edges in through holes. They are made from soft, flexible silicone, ensuring complete coverage and preventing coating penetration.
Typical Masking Situations
- Masking leading threads and chamfers in powder coating and anodizing
- Protecting exit threads in weld nuts to prevent post-process cleaning
- Providing a leak-proof fit for precision-machined components
- Withstanding high temperatures and chemical exposure
5. Silicone Thread Plugs

Design and Functionality
Silicone threaded plugs are designed for blind holes requiring an internal seal at the leading thread or chamfer. Their compact size and precise fit ensure a clean masking result, while the handle allows for easy placement and removal.
Typical Masking Situations
- Protecting leading threads in blind holes in powder coating
- Preventing coating buildup inside threaded holes
- Accurately masks the chafer, but not then surrounding surfaces
- Withstanding repeated exposure to high-temperature curing
Silicone Caps: Types and Applications
1. Standard Silicone Caps

Design and Functionality
Standard silicone caps are designed to cover and protect exposed bolts, studs, and tube ends from coatings. Their flexible nature allows them to fit snugly over various diameters while resisting heat and chemical exposure - this is the most used masking cap by far, and available in a broad range of sizes.
Typical Masking Situations
- Masking bolts, studs, and tube ends in powder coating and plating
- Preventing coating penetration on fasteners
- Ensuring secure retention and easy removal
- Offering reusability for multiple coating cycles
> Masking Supply Silicone Caps
2. Silicone Flanged Caps

Design and Functionality
Flanged silicone caps provide enhanced protection by covering not only the external stud but also the surrounding surface area. This prevents any coating seepage around the edges and keeps the contact face clean, e.g. for electrical connections on surfaces.
Typical Masking Situations
- Protecting precision-machined fasteners in high-temperature masking
- Ensuring full coverage over bolts and studs
- Preventing overspray contamination in powder coating and e-coating
- Providing a reliable seal for plating and anodizing applications
Conclusion: Selecting the Right Silicone Masking Solution
Choosing the correct silicone plug or cap depends on the specific requirements of the masking application. Factors to consider include:
- Hole Type: Use tapered plugs for blind holes and pull plugs for through-holes.
- Temperature Resistance: Ensure the material can endure the curing or coating process.
- Ease of Removal: Select pull plugs or caps with handles for quick removal.
- Reusability: Opt for high-quality silicone solutions that can be used multiple times.
For more information, visit www.maskingsupply.com or contact our experts for advice.